In today’s fast-paced, tech-driven world, mobility is key to operational efficiency across industries, particularly for those managing complex maintenance processes. A Mobile Computerized Maintenance Management System (CMMS) extends the capabilities of traditional CMMS software by enabling maintenance teams to access essential data, complete work orders, and manage tasks from their mobile devices—whether they are on the plant floor, in the field, or off-site. This mobility enhances flexibility, boosts productivity, and ensures more responsive maintenance operations.
Here’s a closer look at the significant benefits of having a mobile CMMS application and how it can transform your maintenance management strategy.
1. Real-Time Access to Maintenance Data
One of the most important benefits of a mobile CMMS is the ability to access real-time maintenance data from any location. Instead of being tied to a desktop or office system, maintenance technicians can view asset details, work orders, and equipment history directly on their mobile devices. This instant access empowers teams to make informed decisions on the spot, minimizing delays and improving response times to maintenance needs.
Example: If a piece of equipment breaks down on the production line, the technician can immediately pull up its service history and documentation from the mobile CMMS to quickly identify possible issues and start repairs without needing to return to an office.
2. Faster Response to Work Orders
A mobile CMMS allows maintenance teams to receive, manage, and close work orders in real-time. With instant notifications, technicians can respond to urgent maintenance requests more quickly and efficiently, which helps to minimize equipment downtime and the impact on operations.
Example: Imagine a critical piece of machinery fails during a shift. With a mobile CMMS, the work order is automatically generated and sent to the technician's mobile device, allowing them to prioritize and respond immediately, thus preventing further delays in production.
3. Improved Communication and Collaboration
Maintenance teams often work across large facilities or in remote locations, which can make communication challenging. A mobile CMMS bridges this gap by allowing technicians, supervisors, and managers to communicate in real time. They can share updates, receive instructions, and even upload photos or videos to clarify problems, all within the app.
Example: A technician working on a remote wind turbine can upload a photo of a faulty component directly through the CMMS app, allowing a senior engineer in another location to review it and provide immediate guidance on how to proceed.
4. Enhanced Productivity and Efficiency
With a mobile CMMS, technicians spend less time on administrative tasks and more time performing actual maintenance. Instead of walking back and forth between work sites and offices to gather information, they can instantly log completed tasks, update inventory, or check equipment documentation on the go. This streamlined workflow reduces time wastage and improves overall productivity.
Example: A technician can complete a repair, log the details into the mobile CMMS, and move on to the next task without returning to the office to fill out paperwork or enter data into a computer.
5. Offline Functionality for Remote Sites
Many mobile CMMS applications offer offline functionality, allowing technicians to access essential information and record updates even in areas with poor or no network connectivity. Once the device reconnects to a network, the data syncs automatically, ensuring that no information is lost.
Example: A field technician working on remote oil rigs or far-flung construction sites can still update maintenance logs or access critical equipment information, even in areas with spotty or no signal, knowing the information will be saved and synced later.
6. Accurate Data Entry and Immediate Reporting
Data accuracy is crucial for effective maintenance management. A mobile CMMS reduces the chances of human error by enabling technicians to input data immediately after completing tasks. There’s no need to rely on memory or manual paperwork, which often leads to inaccuracies. By capturing data on-site and in real-time, a mobile CMMS ensures maintenance logs and work order statuses are up to date and accurate.
Example: Technicians can use their mobile CMMS to scan equipment barcodes or QR codes to pull up the exact details and record maintenance actions directly, reducing the risk of mislabeling or incorrect data entry.
7. Efficient Spare Parts and Inventory Management
Managing spare parts inventory efficiently can be a challenge, especially when parts are located in different warehouses or facilities. A mobile CMMS provides real-time access to inventory data, allowing technicians to check the availability of parts on the go. If a part is needed for a repair, technicians can quickly verify whether it is in stock, reducing downtime caused by waiting for parts to arrive.
Example: Before starting a repair, a technician can check the mobile CMMS to confirm that all necessary parts are available at the closest location, preventing delays due to missing components.
8. Better Regulatory Compliance and Audits
In industries where regulatory compliance is mandatory, a mobile CMMS helps ensure that all maintenance activities are documented accurately and promptly. Technicians can record inspections, safety checks, and compliance-related activities in real time, providing a clear and auditable trail of maintenance history. This also simplifies the process during audits by offering easily accessible records that meet regulatory standards.
Example: Safety inspections for high-risk equipment can be scheduled and tracked through the mobile CMMS, ensuring that technicians follow standard operating procedures and that all compliance checks are properly documented.
9. Increased Asset Life and Reliability
By improving the speed and quality of maintenance activities, a mobile CMMS helps extend the lifespan of assets and enhances their reliability. With regular inspections and preventive maintenance tasks efficiently managed via the mobile app, equipment is less likely to experience unexpected breakdowns. This leads to fewer costly repairs and better asset performance over time.
Example: A technician can receive a preventive maintenance task notification for an HVAC system on their mobile CMMS and perform the maintenance before a critical failure occurs, increasing the system’s efficiency and prolonging its operational life.
10. Data-Driven Decision Making
A mobile CMMS not only facilitates maintenance management but also provides valuable insights through real-time data collection. Technicians can capture asset performance metrics, which are then available to managers for analysis. This data helps identify trends, optimize maintenance schedules, and improve long-term decision-making.
Example: By analyzing data from the mobile CMMS, managers can identify underperforming assets and prioritize replacements or upgrades, leading to more efficient use of resources and better long-term planning.
Conclusion
The mobility offered by a CMMS application is revolutionizing maintenance management by enabling maintenance teams to work smarter and faster, regardless of their location. From improving communication and productivity to ensuring data accuracy and compliance, a mobile CMMS significantly enhances both operational efficiency and asset reliability. With real-time access to data and the ability to manage tasks on the go, organizations can reduce downtime, lower costs, and improve safety across their operations.
In a world where time and precision matter, having a mobile CMMS can give your maintenance team the edge they need to stay ahead of the competition.
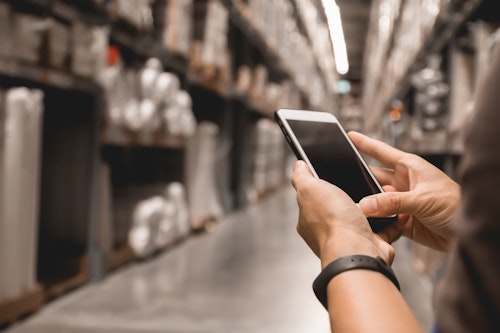
CHAMPS Software