While there are countless KPIs to be monitoring it’s extremely important that we know what KPIs are critical to business and which are not, allowing for a better evaluation of priorities. Before we examine the different types of KPIs, it is important to understand what they are and how they help your business succeed.
What is a KPI in the Maintenance World?
A KPI, or key performance indicator is simply a measurement of how well a task is performed. KPIs can be set for machines, people, or any number of systems. The main goal of a KPI is usually to save money, increase productivity/efficiency, and improve safety measures.
Metrics are in the same family, but a slightly different meaning. Metrics are just a system of measurement. When using both terms together, metrics are the numbers that measure progress towards a goal, while KPIs are the numbers you are aiming to hit.
Where to Focus
Your KPIs should be centered around three major things: strategy, improvements, and long-term growth. When trying to improve these factions of business, it is important to make sure that your goals are both realistic and sustainable. However, the most important thing to remember when setting your goals is to keep them realistic. If your goal production is too high or not sustainable then this can lead to disorganization later on. Another point to keep in mind is that at any given time, you should be focusing on no more than five KPIs.
The Five KPI Rule
After five KPIs, tracking tends to get a little crowded. KPIs are supposed to be high priorities, not simply any metric you want to measure. Your KPIs will change over time, especially with growth, making your goals change with it. When deciding which KPIs you wish to pursue it is highly important to converse with maintenance managers. They are the ones that deal with metrics and keeping production running smoothly on a daily basis. The insight provided by these workers is extremely valuable when crafting KPIs. Below I’ve listed several key performance indicators that would be beneficial to explore. There are many more KPIs out there, however for the majority of companies these will be the most relevant.
MTBF (Mean Time Between Failure)
Mean time between failure is the average time one piece of equipment breaks down (or fails in some capacity) until the next machine failure. MTBF is measured in hours and calculated by the following formula:
MTBF= Total Uptime / Number of Breakdowns.
As a company it should be a goal to lengthen the time between these failures. In order to increase your MTBF you must first make sure your CMMS is capable of tracking these metrics (schedule a demo to see how CHAMPS accurately collects these critical metrics). Then, we must take this data and be proactive, or in other terms, perform preventive maintenance. These routinely scheduled maintenance checks will save far more in the long run than simply performing repairs only after breakdowns.
PM Compliance
PM compliance is one of the most important KPIs you’ll track. It measures how successful your facility is at completing preventive maintenance tasks, as well as how the completion of these tasks has optimized performance. These measurements include optimizing your schedule, reducing downtime, as well as increasing general efficiency. The PM compliance formula is as follows:
PM compliance = # of completed PMs + # of scheduled PMs x 100
In order to improve PM compliance percentage you must make sure that preventive maintenance is on track. In order for this to occur PMs must be made easier to complete. With a trusted mobile software, PMs are now easier than ever!
MTR (Mean Time to Repair)
MTR or Mean Time to Repair measures the average time from the moment a machine breaks down or fails, to the moment it is repaired. It deals with equipment diagnosis, planning, scheduling, and the actual work necessary to fix the machine. Your company’s goal would be to reduce the MTR over time.
Wrench time
Wrench time is defined as the metric that shows how much time maintenance professionals spend with a tool in their hand, actually performing maintenance tasks. Wrench time measures only the time spent doing the work, meaning that time spent picking out tools, travel time, breaks, looking over the work order, etc. are not included. This gives a more accurate measure of time spent purely on manual maintenance tasks.
Percentage of Work Covered by Work Order
This KPI lets you see how much of the maintenance work is entered into your system. This KPI is extremely valuable, as it deals with data collection. It’s important that your maintenance team enter every task in your CMMS system, as this allows for more data, and more data leads to better understanding of patterns and trends, allowing for more accurate predictions of when preventive maintenance should be scheduled.
How to Track Your KPIs
In order to track KPIs effectively it is important that you have a reliable and accurate CMMS system. CHAMPS has an easy to use interface and a mobile component that will make tracking KPIs easier than ever. You’ll be able to choose the KPIs you wish to monitor right on your dashboard.
So what are you waiting for? CHAMPS is dedicated to helping maintenance professionals reach their full potential. Contact us to learn how CHAMPS can help your maintenance team hit their KPIs more efficiently.
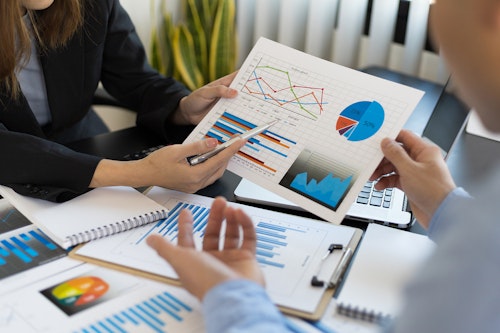
CHAMPS Software