Have you ever been asked to do more with less? It seems that nearly every maintenance organization has faced this challenge at some point. It seems cruelly ironic that some organizations prefer to run their maintenance teams till they break. This type of decision making can be avoided when a maintenance program has been optimized.
Is your maintenance program optimized? You can start your self-evaluation with 3 basic questions. Let’s make your path forward as clear as the benefits of optimization.
Does justification come easy?
Experience is a valuable commodity. An experienced maintenance manager can see the backlog, schedule, and resources and have a good understanding of what can be done and what can’t. They can fairly accurately predict the impact of modifying any of those variables. The challenge is that experience alone does not sufficiently provide justification for many decisions. Reliable data on the other hand is usually cited as one of the most effective methods for justifying a course of action.
Does this form of justification feel difficult or easy? Will justifying your decision through your CMMS be time consuming and complicated? Are you distrustful of the data in your CMMS? These are major road blocks for optimization but they are not insurmountable.
When a maintenance program is optimized justification is easy. At times the data for justification will even precede the awareness of the need. An optimized maintenance program is fine tuned. It operates, pardon the pun, like a well-oiled machine. Even minor adjustments to schedules, work load, team size and the like are clearly reflected in the bottom line.
A well-designed CMMS will make this type of insight easily accessible. Data visualizations, predictive and forecasting functions are all features that make answering important business justification questions easier. Even if your CMMS is not fully equipped with these features there is no need to despair. Data analysis tools can leverage your existing data and turn it into actionable information. When you bring together CMMS process knowledge and data analysis expertise the path toward maintenance optimization immediately becomes a clear and achievable goal.
How good is my CMMS at estimating?
Walking down the midway at a carnival you might pass a vendor who wants to guess your age. They are willing to reward you with a prize if they cannot guess within a certain degree of accuracy. These individuals are trained to make quick observations and guess based on averages. On the other extreme, there are scientists who employ sophisticated techniques based on the half-life of particular elements to date ancient artifacts.
One of these forms of estimating is a parlor trick, the other a serious evaluation. Which does your CMMS more closely resemble when it comes to estimating?
There are many areas within a CMMS that allow for estimating. Therefore, we will focus on the most common, Preventive Maintenance, for the sake of simplicity.
A CMMS typically provides the ability to estimate labor and material costs on a PM. How accurate are yours? If you find your estimates completely unreliable your ability to optimize may be severely hampered. A question to consider is how did these estimates become worthless? Was it because you never made use of the feature in the first place? Is it because keeping up with this data is tedious?
If, on the other hand, you feel that your PM estimates the question could be asked how do you know? Some CMMS applications provide functions for updating a PM with a more realistic depiction of work. However, not all CMMS are created equal in this regard. Is the function mostly automated or mostly manual? Does the process accommodate PM work that may have been included in a larger work package? Does the CMMS give you the tools to trend this data?
You will see a ripple effect of measurable improvement throughout the department as your PM program becomes optimized . This will come the form of schedule compliance, wrench time, and material ordering and availability.
Optimization of this kind is not possible in every maintenance department. Many managers struggle with even minor improvements in accurate estimating. In our next post we will discuss one more basic question related to optimization.
Does my maintenance program know how to identify a bad PM?
The preventive maintenance (PM) plan is the heart of a good maintenance program. They are essential to maintain the smooth operation of your work environment and reliability of your equipment. However, this does not mean that all PMs are good. Could you have bad PMs at your facility? How would you identify them? Let’s start with a basic definition of what we’re looking for that makes a PM bad.
What is a bad PM?
A bad pm is redundant, prohibitive, and not critical.
Redundant PMs can easily sneak into a CMMS. They can come about from changing your maintenance strategy, personnel, and even CMMS application. User error can create redundancy. That’s why you should always be careful when adding or changing frequencies. Whatever the case, a redundant PM is a bad PM.
When you initially created your PMs cost was an important factor. However, costs associated with labor and materials will escalate with time. Hence, even a well-designed PM can eventually become cost prohibitive.
Has non-critical equipment found its way into your PM program? Some confuse the concept of Reliability Centered Maintenance (RCM) for reliability at all costs. A bad PM is focused on non-critical assets.
An optimized maintenance program identifies bad PMs and saves money
When your maintenance program is optimized a bad PM stands out. A good CMMS will help you evaluate cost trends of your PM program based on criticality. Therefore, assets with high costs can targeted for improvement. In a good solution repair vs replace costs are obvious. Removing bad PMs creates instant measurable savings to your bottom line.
CHAMPS is dedicated to helping maintenance organizations reach their full potential. Contact us to learn how CHAMPS can help your maintenance organization to become optimized.
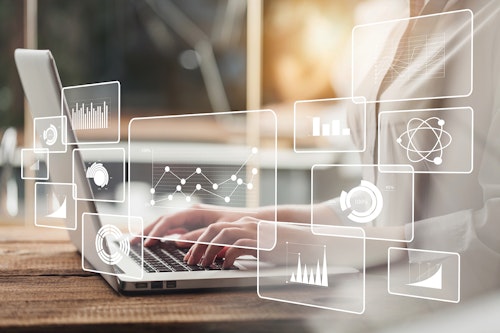
CHAMPS Software