Lockout/Tagout, or LOTO for short, is a process many of us are familiar with. Put in place to prevent accidents and ensure worker safety, LOTO is often used in conjunction with regulatory bodies like OSHA to ensure that no corners are cut and all work is performed according to any applicable regulations and standards.
Naturally, the next step in improving LOTO will be implementing automation to help streamline the process even further. Here, we’ll explore the benefits of automating your LOTO process as well as what to look for when choosing the right LOTO solution for your organization.
Why do we use LOTO?
The primary purpose of LOTO activities is to prevent accidents, save lives and protect equipment from extensive damage. The most important requirement for any overhaul and maintenance operation is the safety of the workers. This is the reason why there are outage planners and OSHA regulations for locking and tagging procedures. These procedures, accompanied by compliance regulations, are commonplace for many companies and dealt with on a daily basis. This could cause these life saving activities to be viewed as routine. Thus, they may not be receiving the constant attention that they deserve.
Your LOTO routine
When something is viewed as a routine, it is often difficult to improve the process. Routine suggests an already established course, whereas improvement changes direction. In terms of safety, a change in direction may raise warning flags in your mind, which is a good thing. If a process is working, you are inclined. The most important requirement for any overhaul and maintenance operation is the safety of the workers to keep it that way. But, what if there were a better way? What if potential errors could be prevented? What if accidents could be eliminated? What if lives could be saved? Wouldn’t these possibilities at least warrant further consideration? To find a better way, let us first look at what is typically considered the ‘routine’. To start with, we will look at the overhaul, repairs or maintenance work. This work emerges in the form of work orders generated for the operations and maintenance department. This may come directly from a CMMS. Whether planned or not, if this work requires locking and tagging of equipment, it will eventually need to transfer to a boundary planner or someone in operations. Here is where the safety aspects of the work begin. First, isolation boundaries are created. These will need approval. The next step is performance. Tags are printed and hung in the field and then independently verified. Once work is authorized, the maintenance department takes it over as approved work that is ready to be performed. Workers then sign on and off of work packages, perhaps at a specific physical location like a tagging desk, as the work is completed. Finally, at the conclusion of this work, tags are cleared and normal operations resume. This entire process requires many information transactions. These transactions come in the form of paperwork, electronic data or a combination of both. Proper management and distribution of this information is what keeps your plant workers safe. While the traditional LOTO process is effective, there is a way to make this entire effort better, quicker and ensure that your equipment and workers are even safer by completely automating the process.
Automating the process
To automate the LOTO process, finding the right software solution is obviously the key to your success. One common area of concern is your IT Infrastructure. A lack of personnel may have prevented a CMMS solution from being implemented. While a LOTO application will likely take less support, IT support may continue to be an area of concern. Similarly, infrastructure integration plays a major role in any software purchase. Details from platforms and operating systems to network and hardware requirements all have to be considered. This level of infrastructure integration can be labor intensive for many organizations. Is that the case with yours? Data migration and entry are also involved. No safety application is simply ‘plug and play’. What kind of commitment of technical resources is your company willing to make? Of course, LOTO applications can be, and are, implemented without work control software. Most operate in an independent manner by providing their own equipment and/or device records and personnel records for locking and tagging activities. Even without CMMS or EAM integration, automating LOTO brings many benefits. However, the benefits are significantly increased when these applications work together.
Commitment to a process is absolutely critical. So, before you decide on which application, you should first secure commitments from all your groups. Does your company see the need for a change? Are your planners and operations personnel prepared to support a software solution even if it means drastically changing their current process? Total buy‐in is unrealistic, but a general sense of commitment is not.
LOTO and CMMS
LOTO applications with this feature will allow your work to be performed faster and safer by being directly linked with work orders. It is not uncommon for a LOTO application to claim integration with a variety of CMMS applications. However, there are many different levels of integration. Their integration may simply reference a work order number to a tag. So look to establish what level or integration you’re trying to achieve. Does your integration include identifying isolation boundaries on individual pieces of equipment? Do you want your LOTO software to cross-reference tags not only to work orders, but down to their individual steps and each worker signed into that step? There are LOTO applications that can do this. This type of functionality makes the most of a CMMS to LOTO application integration.
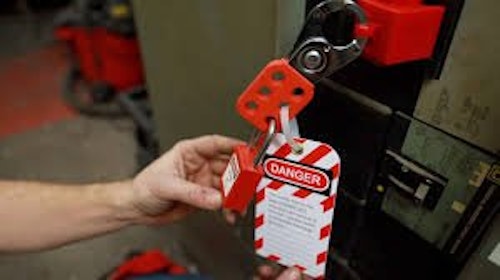
CHAMPS Software