If your maintenance team has the opportunity to be 100% efficient and productive wouldn’t you take it? It’s something that seems superfluous, but it remains the ultimate goal of any organization who decides to implement Total Productive Maintenance.
TPM is a unique method of maintenance that involves machine operators in the maintenance process of the equipment they operate. It is applicable across several industries, however it is most commonly used in the manufacturing sector due to its radical and unique approach to maintenance.
In manufacturing, TPM primarily focuses on equipment effectiveness, which aims to determine the percentage of production time that is productive. The goal is to track progress towards “perfect production”, with scores ranging from as low as 40% for inefficient systems, to 100% for perfect systems.
What Are the Goals of TPM?
TPM is based upon achieving certain goals such as:
- A proactive (see proactive vs. reactive) approach to maintenance with shared accountability for equipment care
- Employees at all levels in the company are involved in the maintenance process leading to decreased downtime
- No equipment defects and zero downtime
- Achieving zero accident levels and creating a safer work environment
- Low waste in the production process
- Improving product quality
What Are the Benefits of TPM?
Businesses that strive for perfection and employ TPM can reap the following benefits:
- Team members are empowered and encouraged to maintain their machines giving them a sense of “ownership”
- Minor maintenance issues are brought to attention and fixed faster, without waiting for the assessment of the maintenance technicians
- Improved productivity due to fewer breakdowns and stops
- Improved quality and customer satisfaction
- Lower manufacturing cost
- Fewer accidents in the work process
The 5S
Implementing Total Productive Maintenance begins with creating a solid foundation on which to build. The foundation is achieved by implementing the 5S methodology.
5S stands for:
- Sort – Seek useful items and eliminate those that are not required. It makes work easier by removing obstacles and reducing the risk of disturbance from distractions.
- Set In Order – Organize new space and remaining items. Tools, equipment, and other resources are well-arranged and in close proximity when needed.
- Shine – Clean and inspect work area. The workplace is safer, better to work in, and equipment is better kept.
- Standardize – Record and enforce standards for the above steps. Establish consistency and make it a part of the daily schedule.
- Sustain – Apply standards frequently. Carry out regular audits, training, and discipline and be open to feedback and suggestions for improvements.
How Can a CMMS Help with Total Productive Maintenance?
A quality CMMS system can aid in implementing Total Productive Maintenance in many ways. It allows for more autonomous maintenance, more planned maintenance, focused improvement, better education and training, and improved quality management.
One of the major ways to increase TPM is by investing in a CMMS software that helps keep everything on track. A good CMMS will not only increase Total Productive Maintenance, but will help you target other KPIs as well. To learn more about how CMMS can help with your scheduled maintenance, call us at (352)-795-2362 or schedule a demo today!
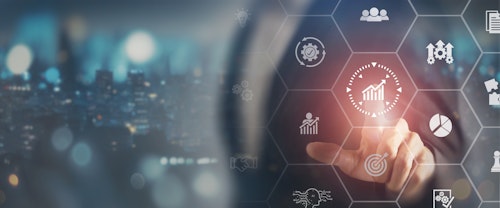
CHAMPS Software